
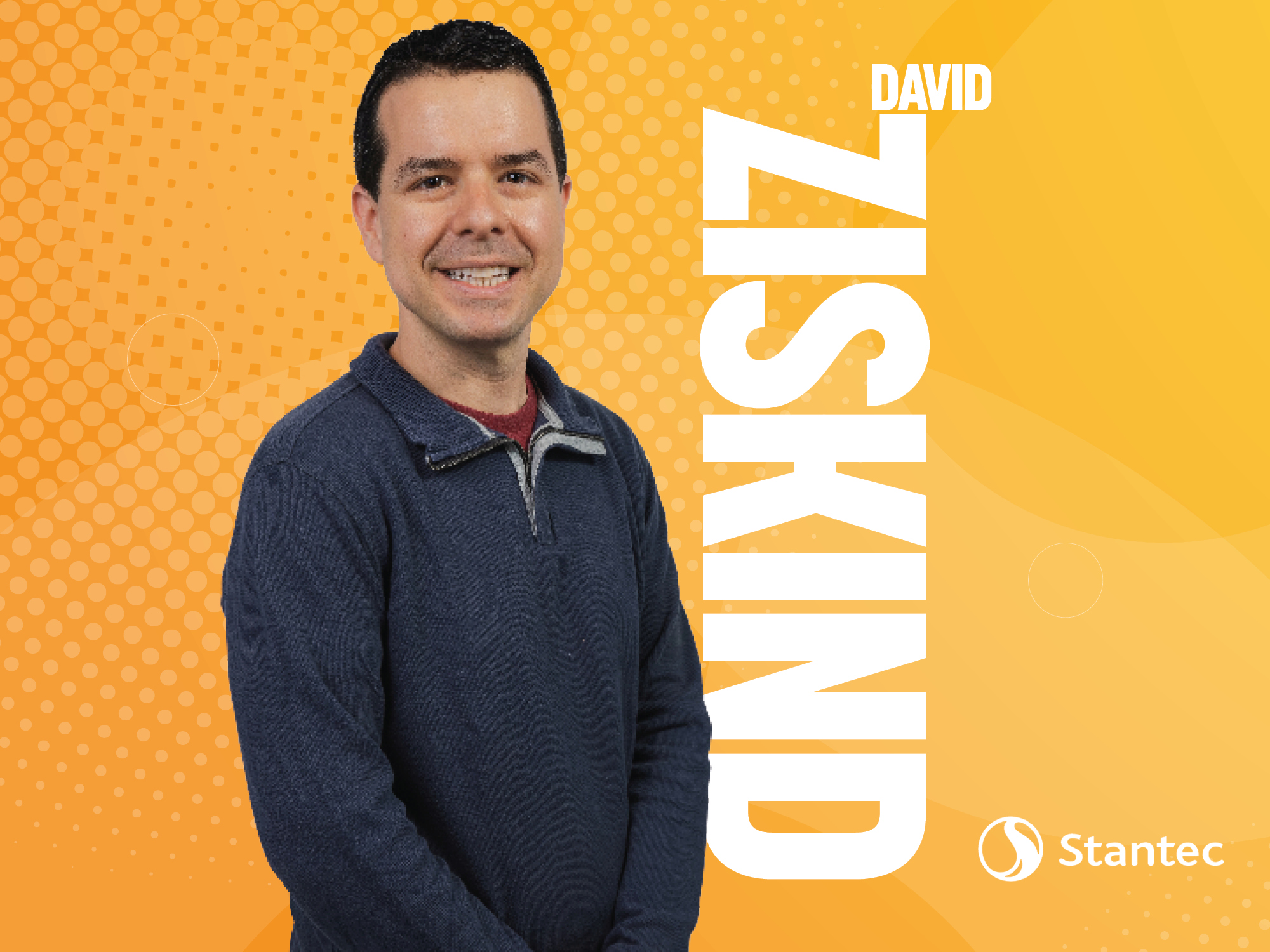
Facility planning in the face of uncertainty
“Measure twice, cut once.” We’ve all heard this phrase. If building something, you probably have precise measurements of what you need. If a piece of wood is required that’s a specific size, it would waste time and money to cut the wrong length. Similarly, if manufacturing a known product, we probably have a good idea of the process and facility needs, and can design and build accordingly. What about the scale-up of a new or novel food, involving a nascent process such as precision fermentation or even cultured meat? We know ‘planning’ is important but how do we apply this in the face of uncertainty?
Perhaps you’re familiar with the saying, ‘Good, fast, cheap – pick two’. Or the project management triangle balancing scope, cost, and schedule. Let’s consider we don’t have to select one characteristic over the other. Sure, we could wait until every single variable has been tested and confirmed, and we proceed with absolute certainty. What is that cost, both financial and time to market? By the time it is fully defined, our competition has already become entrenched. Conversely, we could move as fast as possible, but what would that financial cost be in terms of rework?
The planning process is our best chance for influence. There is a cost-influence curve that is generally inversely plotted against time, the project life-cycle. Early in the project (during early planning), your influence is highest when your cost is lowest. At some point, though, these curves cross – you’re committed in terms of procurement and construction – and ability to influence decreases as costs go up. Not a good time to make major changes!
What can we learn from this? Scope definition is vital. Iterate early and often, when the cost is lower. Spending time in planning and definition increases certainty and decreases costs later. Changing later in the project obviously costs more. True, we may not have all the answers or know exactly how the process is going to scale-up. Still, let’s ensure we methodically go through the planning process and don’t skip steps. Move as quickly as you need to, but don’t skip steps! Go through the feasibility process, including developing a project charter, establishing an execution strategy, and getting stakeholder alignment. Spend the time to align on strategy and go through a master planning exercise, and then move on to conceptual design, where you can use the project charter and master planning ideas to start framing the project.
We have to balance the plan with cost and speed, acknowledging that we may have to give a little in one area to gain in another
The design basis becomes a key document, where you capture assumptions and constraints. We know there will be a certain level of uncertainty throughout, but be sure to document it, and iterate back through as circumstances change, breakthroughs occur, or additional data becomes available. Again, document all those assumptions so stakeholders are clear on the data you are going in with. With enough heads around the table, you will be able to align on a reasonable range for the uncertainty, all the while balancing with the impact on cost and schedule.
Consider upsizing utilities and systems, especially where the incremental cost of the increase is relatively minor. Better to have that additional space in your layout, ceiling height, electricity, water, heating and cooling capacity, compressed air – whatever the case may be – than to back yourself into a corner where a change in the process system causes a major facility issue. In that case, instead of making an adjustment to just the process system or equipment, you are having to make major changes or concessions with the facility itself.
Sometimes, especially in a schedule crunch, people want to skip directly into detailed design or even execution (let’s go, let’s build this!). We need to respect the importance of moving quickly, while also acknowledging the very real financial (and schedule) cost impact on not working methodically through the planning process. Iterate, but go through the whole definition process. Don’t skip a step especially in the early stages where your influence is higher and your costs are lower.
Given the inherent uncertainty in the scale-up of a nascent process, despite our best attempts, we are unlikely to come up with the perfect set of assumptions when planning a future facility. We have to balance the plan with cost and speed, acknowledging we may have to give a little in one area to gain in another. Ultimately, taking a systematic approach to the planning process will result in better cost certainty, refined schedule, and reduced risk. Higher confidence all around!
David Ziskind is the Market Lead for Food & Beverage at Stantec. Through innovative solutions, he helps companies sustainably solve their manufacturing infrastructure challenges. This article was republished from the July/August 2023 edition of Protein Production Technology International, the industry's leading resource for alternative proteins. To subscribe to read future editions hot off the digital press, please click here
If you have any questions or would like to get in touch with us, please email info@futureofproteinproduction.com
More Opinion
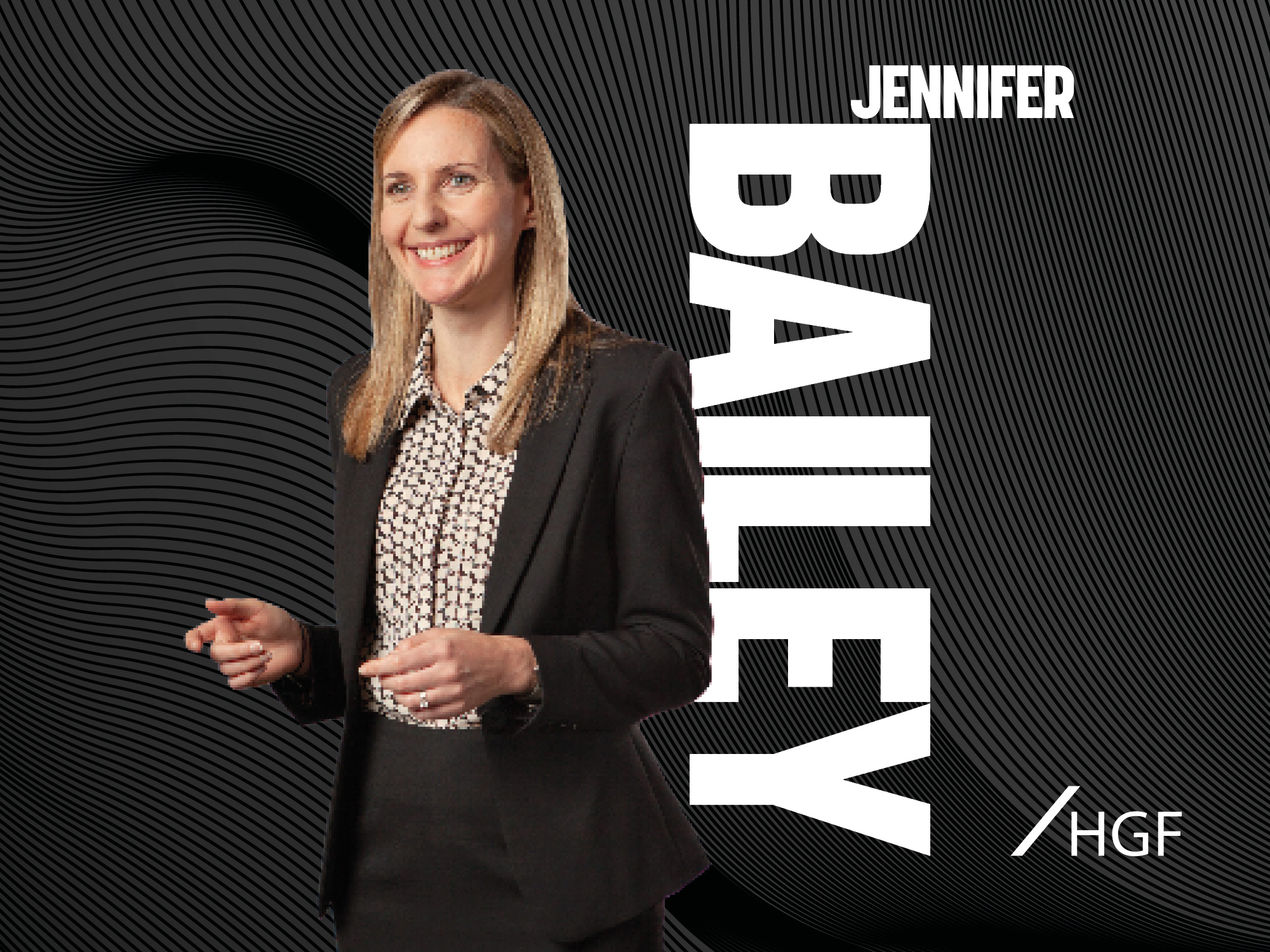
Trade secrets: when, how and why to use them

The criticality of conducting LCAs
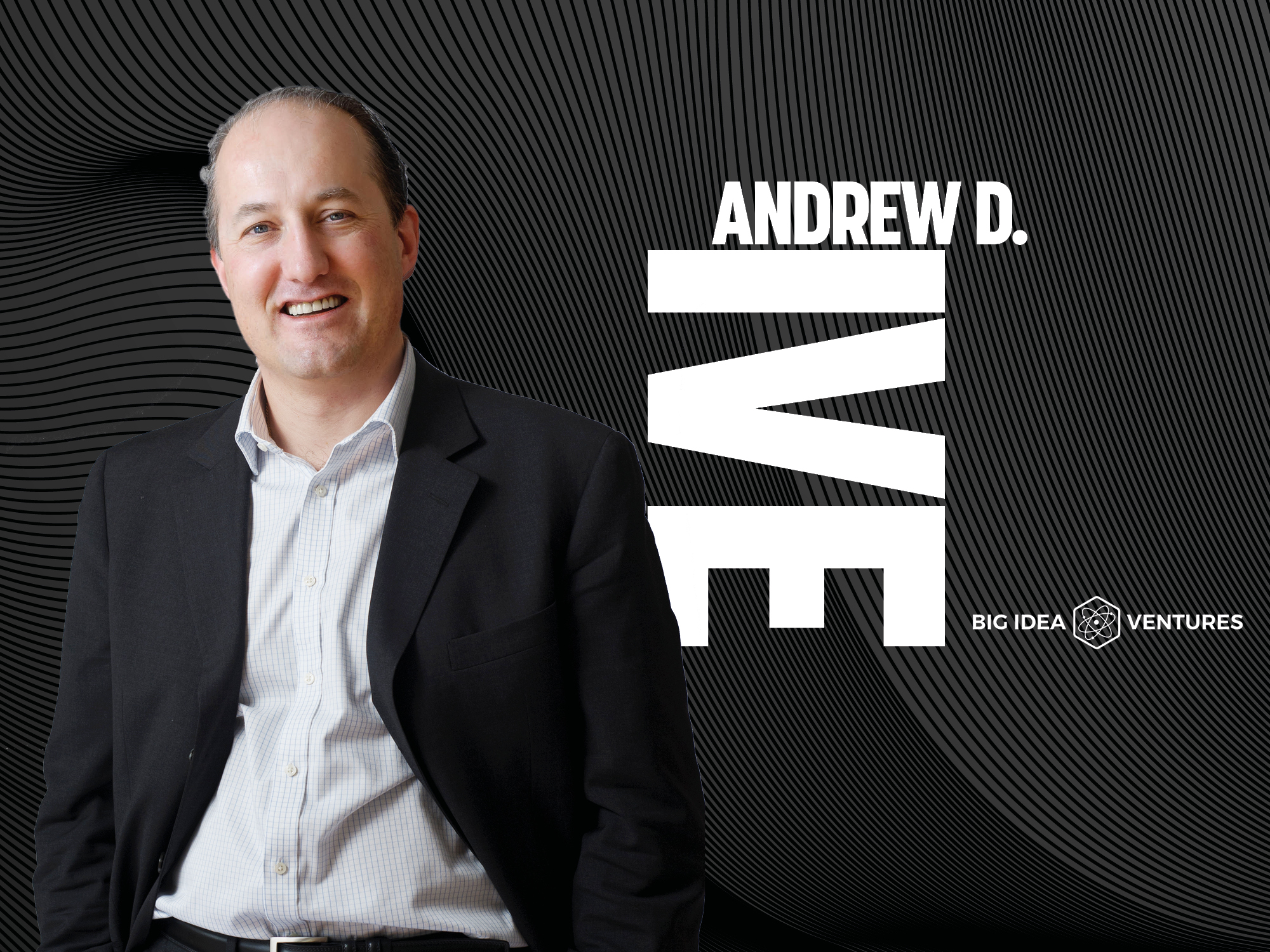
Creating a new protein sector: Part I
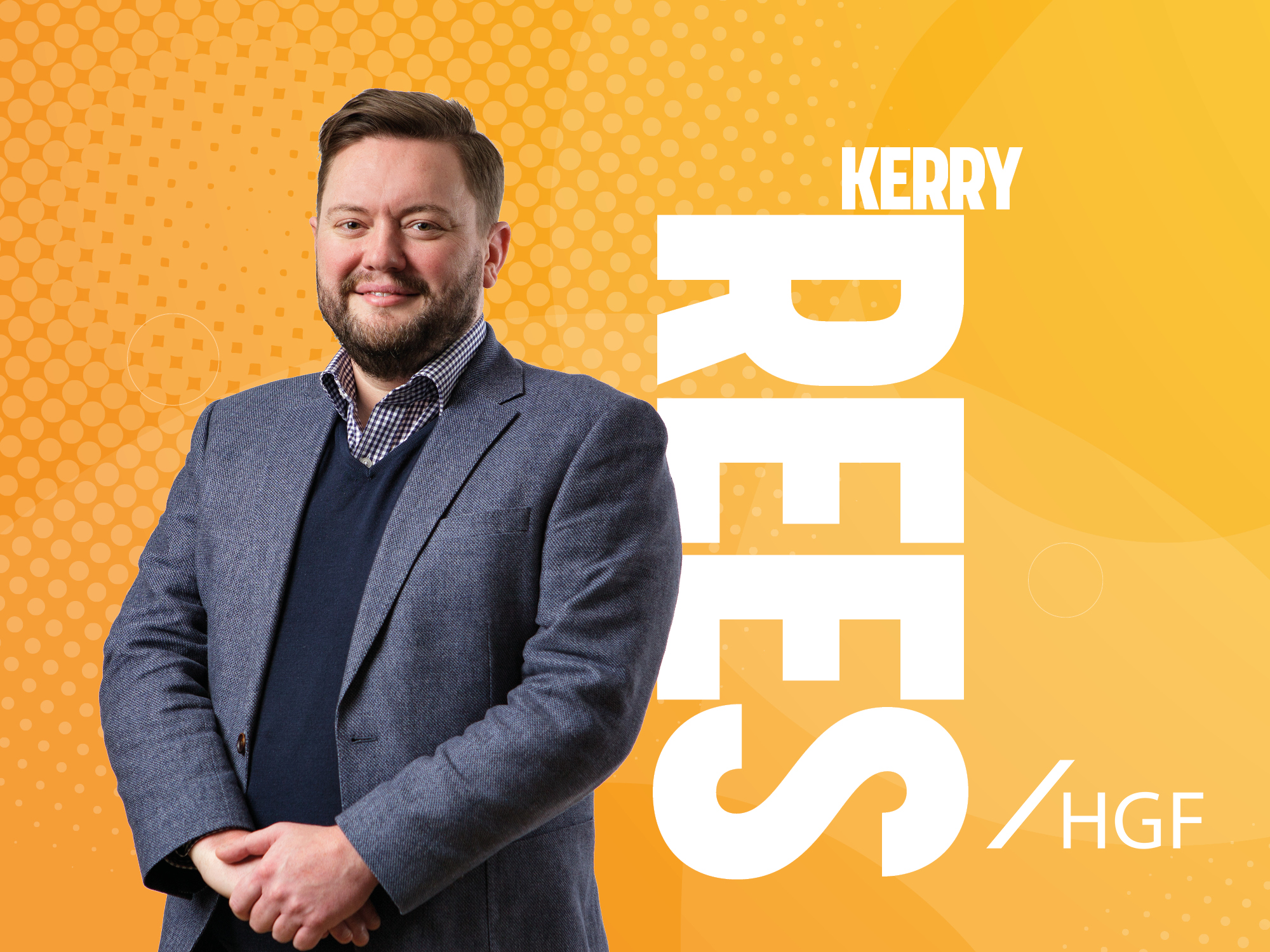
Protecting IP on a budget
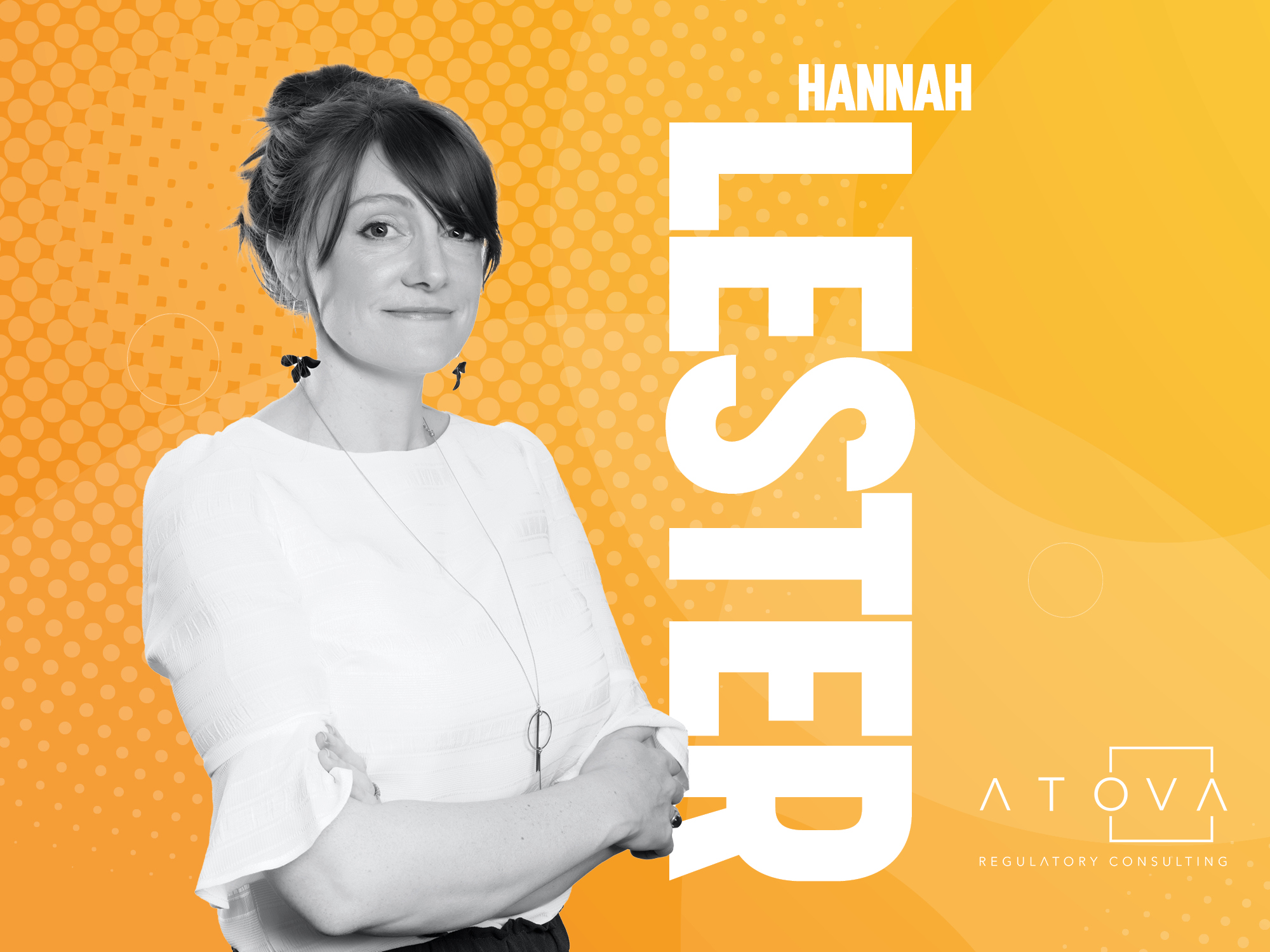
Will the UK become the new Singapore?
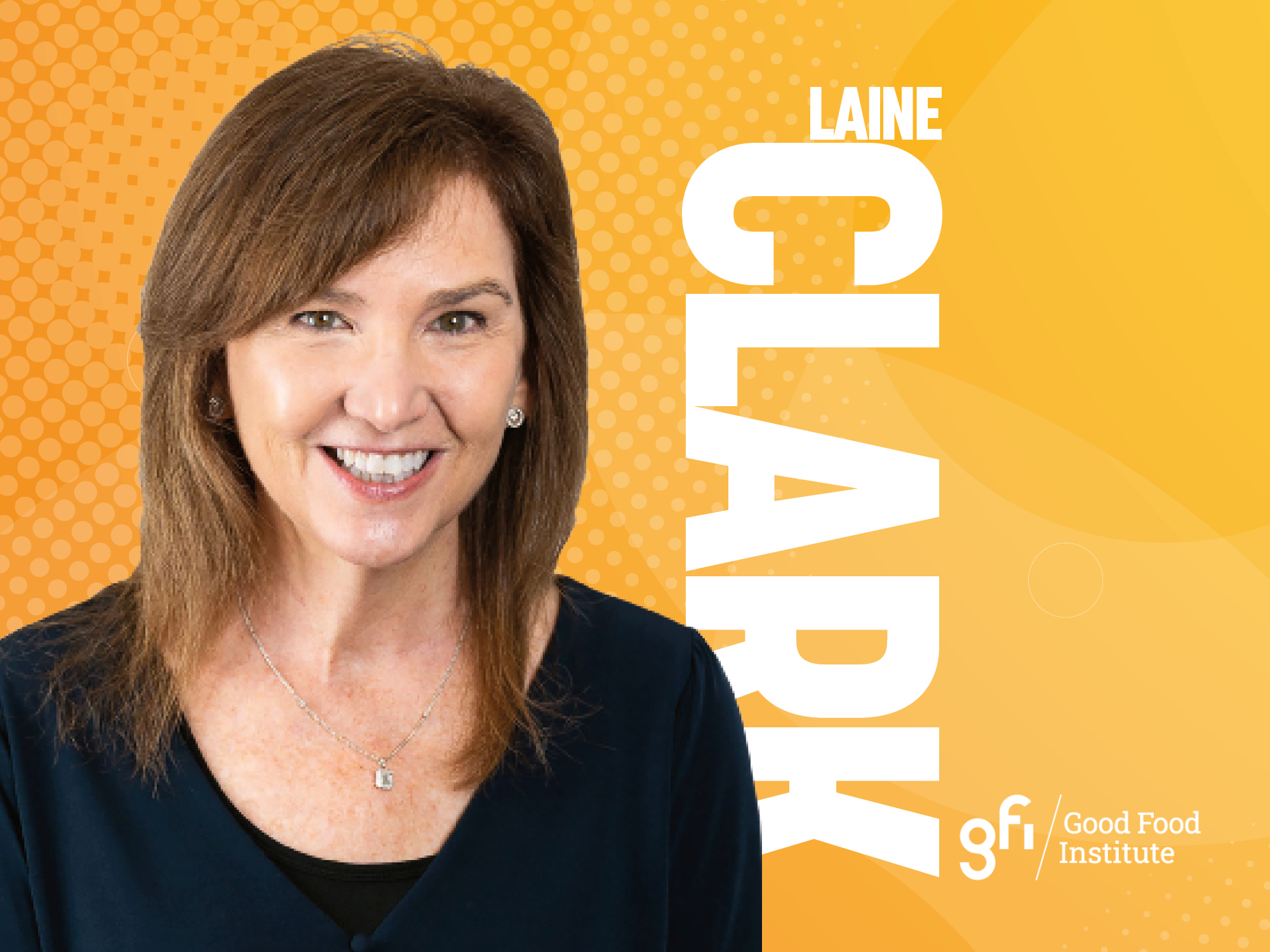