
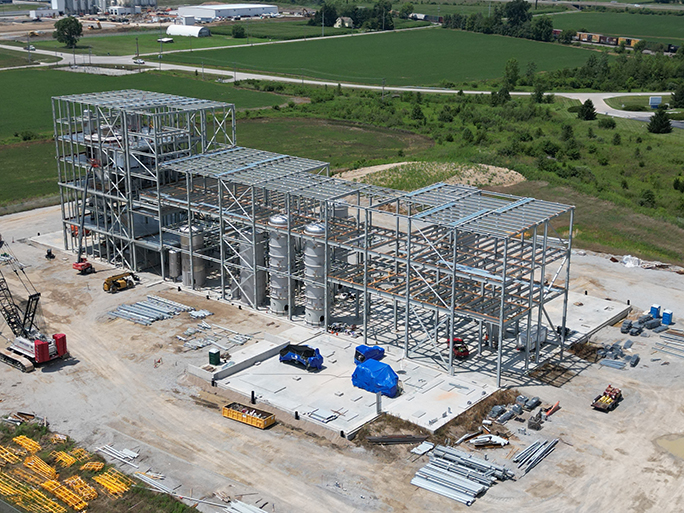
How Liberation Labs’ state-of-the-art facility will bridge the fermentation gap
Liberation Labs, led by Co-founder & CEO, Mark Warner, is expanding precision fermentation capacity to meet the growing demand for alt proteins. With its new facility, the company aims to revolutionize sustainable food production
With the global appetite for sustainable protein sources growing, precision fermentation is one of the tools in the alt proteins box arguably best poised to satiate it. Offering a promising alternative to traditional animal agriculture, it’s a technique that leverages microorganisms to produce specific proteins. By using bacteria, yeast, or fungi, scientists can create a wide range of alternative proteins, fats, and flavors, with applications ranging from alternative meats and cheeses through to supplements and infant formulas. Although the industry is still in its nascent stage, its potential is undeniable.
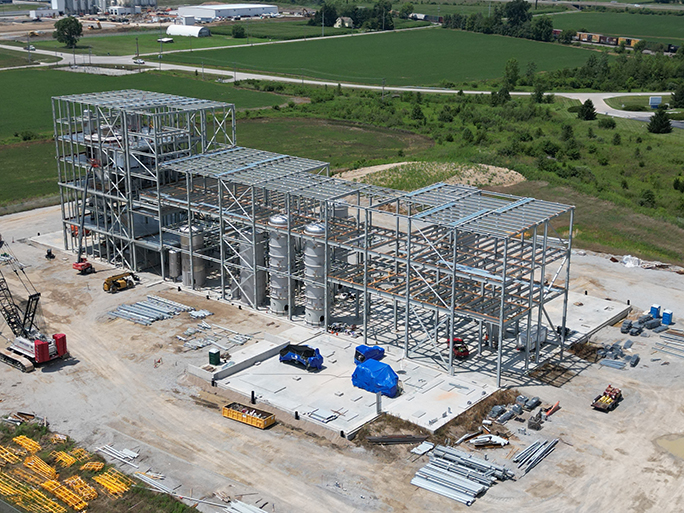
But there are numerous hurdles to overcome if the technology is to realize that potential. The world boasts a substantial fermentation capacity, but much of it is currently dedicated to other sectors such as pharmaceuticals and biofuels. Europe – a fermentation powerhouse – holds nearly half of the global capacity, albeit regions such as North America and Asia are rapidly catching up. In the USA, Liberation Labs is an emerging leader among the companies looking to add to the mix. It is constructing a state-of-the-art biomanufacturing facility in Richmond, Indiana, which has been designed specifically for precision fermentation, enabling the CMO to produce bio-based ingredients at a commercial scale.
Fermentation is an exciting space, with keen investor interest, despite the supposed challenging climate, with some companies in the field – especially those using agricultural byproducts as feedstocks – recently benefitting from some particularly large windfalls. Among those with sizeable injections were ProteinDistillery and Infinite Roots, which scooped €15 million (US$16.5 million) and €53 million (US$59 million), respectively, for scaling up mycoprotein production using brewing byproducts, while Finland’s Enifer also raised €36 million (US$40 million) to operationalize its factory.
In fact, according to Net Zero Insights figures, in the first half of 2024 alone, European companies in the sector raised an impressive €164 million (US$182 million). Leading the charge, biomass fermentation garnered just over €115 million (US$127 million) in investments during the same period, while precision fermentation attracted €49 million (US$54 million).
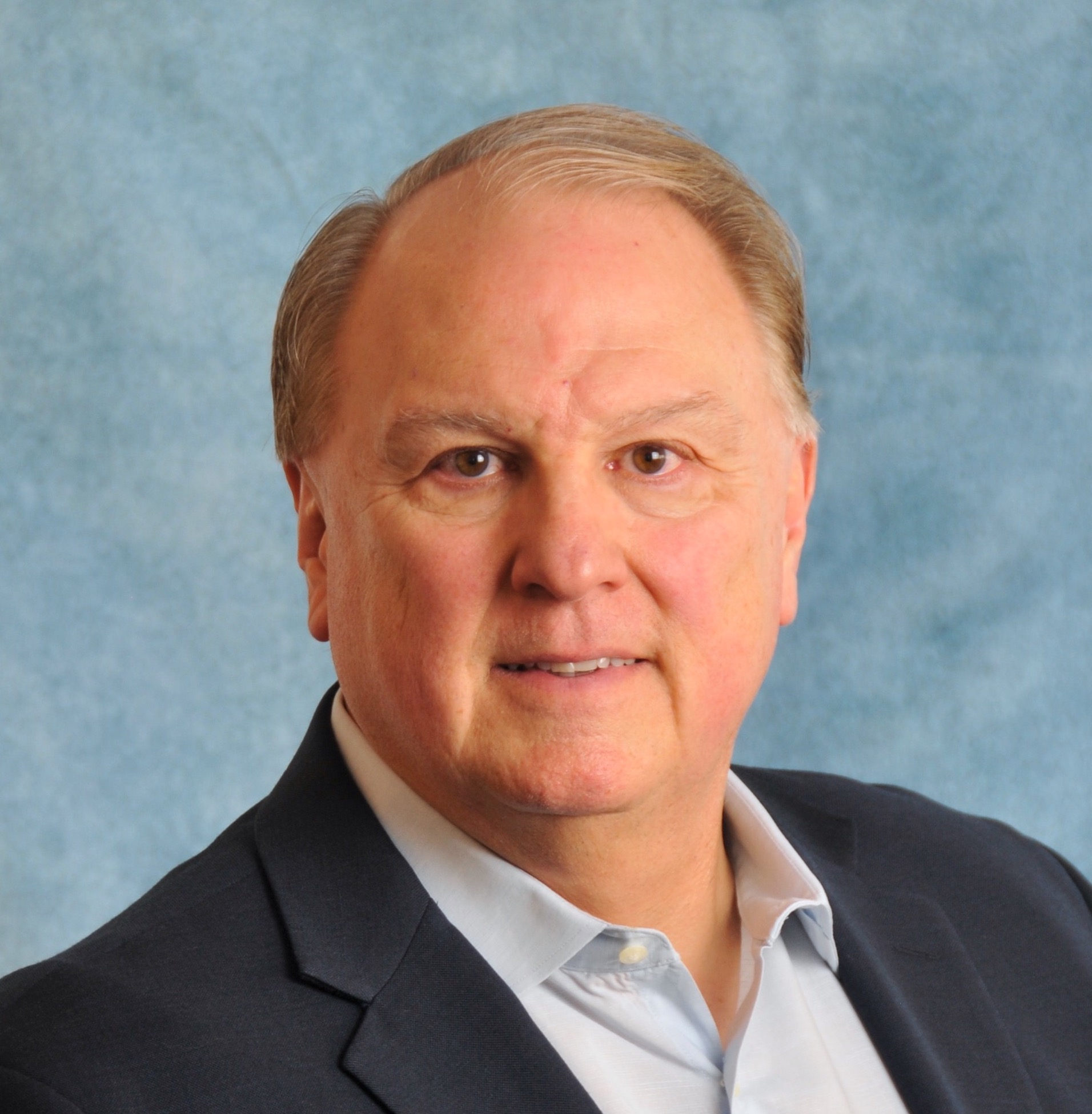
Although funding for R&D and lab-scale companies is vital, the real challenge is in producing these novel proteins at scale at a level of quality and cost that the market expects. “People often only consider total capacity,” notes Mark Warner, Co-founder & CEO of Liberation Labs, “but the problem is that much of the existing capacity is 40-50 years old and built for other purposes like pharmaceuticals and biofuels. So, it’s not well-suited for manufacturing these new novel products. It’s like developing a great app for an iPhone but having to make all kinds of tweaks to get it to run on a flip phone. That’s kind of what’s going on in the industry. R&D often isn’t developing the process they want. They’re having to redevelop the process that can run on the existing network. So, what we’re doing with our Richmond facility is bringing a modern platform that really lets them get the performance they expect from these new strains, which ultimately comes down to cost.”
State-of-the-art facility
Having broken ground in June 2023, recent photos of the construction site are impressive. “The project is progressing smoothly,” Warner enthuses. “We’ve completed about 60% of the work, and of all major equipment has been ordered. We’ve secured environmental permits and finished most of the concrete work. As the recently published pictures show, the main building’s structural steel is in place, and equipment is being installed. We anticipate being operational in the first half of next year.”
This initial facility – which Warner refers to as a ‘launch facility’ – has a capacity of 600,000 liters. “Although it’s profitable, it’s on the smaller side of commercial fermentation,” he admits. “Our goal is to expand to approximately four million liters at the Richmond location. We’re currently evaluating expansion options there, as we have the necessary land and utilities. Ultimately, we plan to build facilities in six regions worldwide. As well as our US plant, we’ve already selected potential sites
While quality is essential, manufacturing cost becomes relevant only if quality standards are met. Our focus on efficiency and high yield allows us to offer a significant advantage in terms of manufacturing cost
The strategy behind this international outlook is to address the concerns of large consumer packaged goods (CPG) companies that, in an ideal world, shouldn’t be relying on a single source for their ingredients, especially if that source is located in a different region. “By having facilities in multiple locations, we can offer both redundant supply and local production, ensuring that companies can launch products in various markets without supply chain disruptions,” Warner confirms.
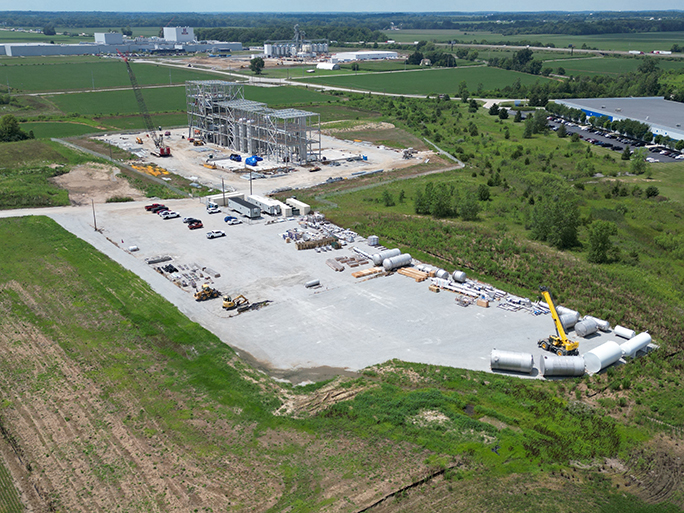
So, how much of a dent will Liberation Labs make in the whole scheme of things? Well, currently, the overall fermentation market has approximately 60 million liters of capacity. Warner’s ambition is to add 25 million liters over the next decade, increasing the total capacity by 40-45%. However, he says it’s important to note that due to the age of existing facilities, more capacity has been retired than built in recent years. “Although our expansion won’t replace all the existing capacity, we believe it will be more than sufficient to meet the growing demand,” he predicts.
It’s difficult to provide a precise figure, but industry experts estimate a significant increase in capacity will be needed to meet the growing demand for alternative protein sources, which ranges from several hundred million liters to potentially billions of liters over the next decade. “Although management consulting studies often suggest a 5-10x increase in capacity, we believe a more realistic range is 2-3x,” Warner says. “This is based on factors such as continued improvements in fermentation technology and the practical limitations of scaling up production. Overall, we anticipate that the industry to double or even triple in size over the next decade.”
A differentiated approach
The Liberation Labs CEO – who was previously Chief Engineering Officer at Impossible Foods – cannot stress enough that suitability is just as vital as capacity, if not more so, which is why the Richmond facility has been designed for modern food production, unlike those older facilities built for different purposes.
“We can produce a wider range of products, including food-grade ingredients, and manufacture the entire product on a single site,” Warner says. “This is unique, as many other facilities rely on multiple locations for different stages of production, which can lead to quality, cost, and sustainability issues. We strategically chose the USA for our initial facility due to the significant gap in capacity for food proteins. Although companies such as Impossible Foods have been working towards expanding into Europe for years, the reality is that food proteins need to be manufactured locally to meet current market demand.”
But for Warner, Liberation Labs’ biggest differentiator is its flexibility as a contract manufacturer. “We designed our facility to accommodate a wide range of processes, making it easy to switch between different products. Unlike many other facilities – which often require significant modifications to produce new products – we are adaptable. That, combined with our efficient and high-performing operations, sets us apart from the competition.”
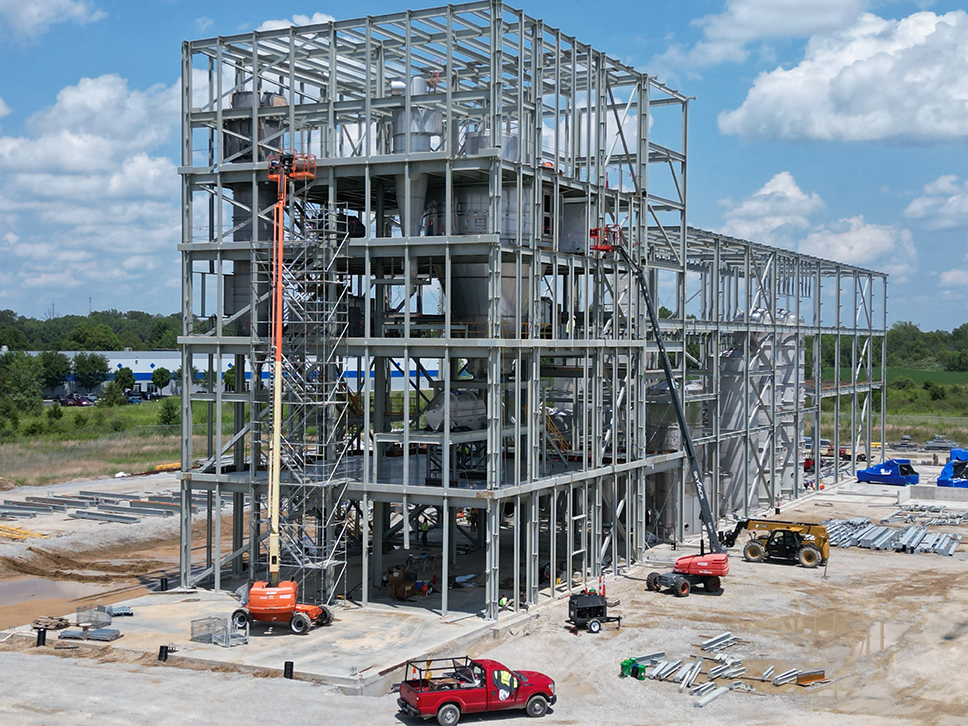
Cost-effective production
Manufacturing costs, especially for well-developed processes, are a major factor in the overall cost of production. Yet although fermentation is often the focus, downstream recovery can be equally important in terms of capital investment and cost contribution. “We’ve optimized our downstream processes to increase productivity, meaning we can produce more product per unit time,” Warner states. “This translates to a lower cost per kilogram, even if our operating costs are similar.”
When evaluating a contract manufacturing organization, Warner says the key metrics are operating costs and product output. “We’ve conducted thorough techno-economic analyses to demonstrate our competitive advantage in terms of unit cost,” he says. “Our ability to produce more product efficiently can significantly reduce the cost per kilogram compared to other facilities.”
And on the topic of fermentation efficiency, he says another key factor is the turnaround time between batches. “We have a rapid turnaround of just 24 hours or less, compared to the 1.5-2.5 days common in other facilities,” reveals Warner. “This downtime reduction directly impacts productivity.”
A further important aspect is ensuring that downstream processing doesn’t limit the fermenters, and in that regard, Warner says he and his team have optimized downstream operations to achieve this, allowing Liberation Labs to produce 30-40% more product per unit time than other processes.
Yield is obviously a critical factor in downstream processing. On that note, many existing processes have a recovery yield of around 70-75%, but Liberation Labs’ process is designed for a higher yield of 85-90%.
“When it comes to KPIs, Warner suggests the most important metric for many of Liberation Labs’ clients is manufacturing cost. “Because quality is essential, manufacturing cost becomes relevant only when quality standards are met,” he says. “Our focus on quality, efficiency and high yield allows us to offer a significant advantage in terms of manufacturing cost.”

a fermentation capacity of 600,000 liters
Liberation Labs is currently in discussions with approximately 30 companies, with eight or nine of those discussions in the advanced stages. “Although food products are a significant part of our pipeline, we’re also seeing increasing interest in non-food applications such as infant formula components and biomaterials,” he says. “In the past, I would have predicted that the first successful product [off the Richmond production line] would likely be a food product for a startup. I still believe it will be a food product, but non-food applications are becoming more prominent.”
Further fueling his excitement, Warner is pleased to see the growing interest from large, traditional companies in his company’s contract manufacturing services. “They may be developing their own processes or partnering with startups,” he notes. “Regardless, these companies ultimately want to make the decisions about manufacturing and be involved in the transactions. This trend is a positive development, as it provides us with more options and stability.”
For more information visit www.liberationlabs.com
If you have any questions or would like to get in touch with us, please email info@futureofproteinproduction.com