
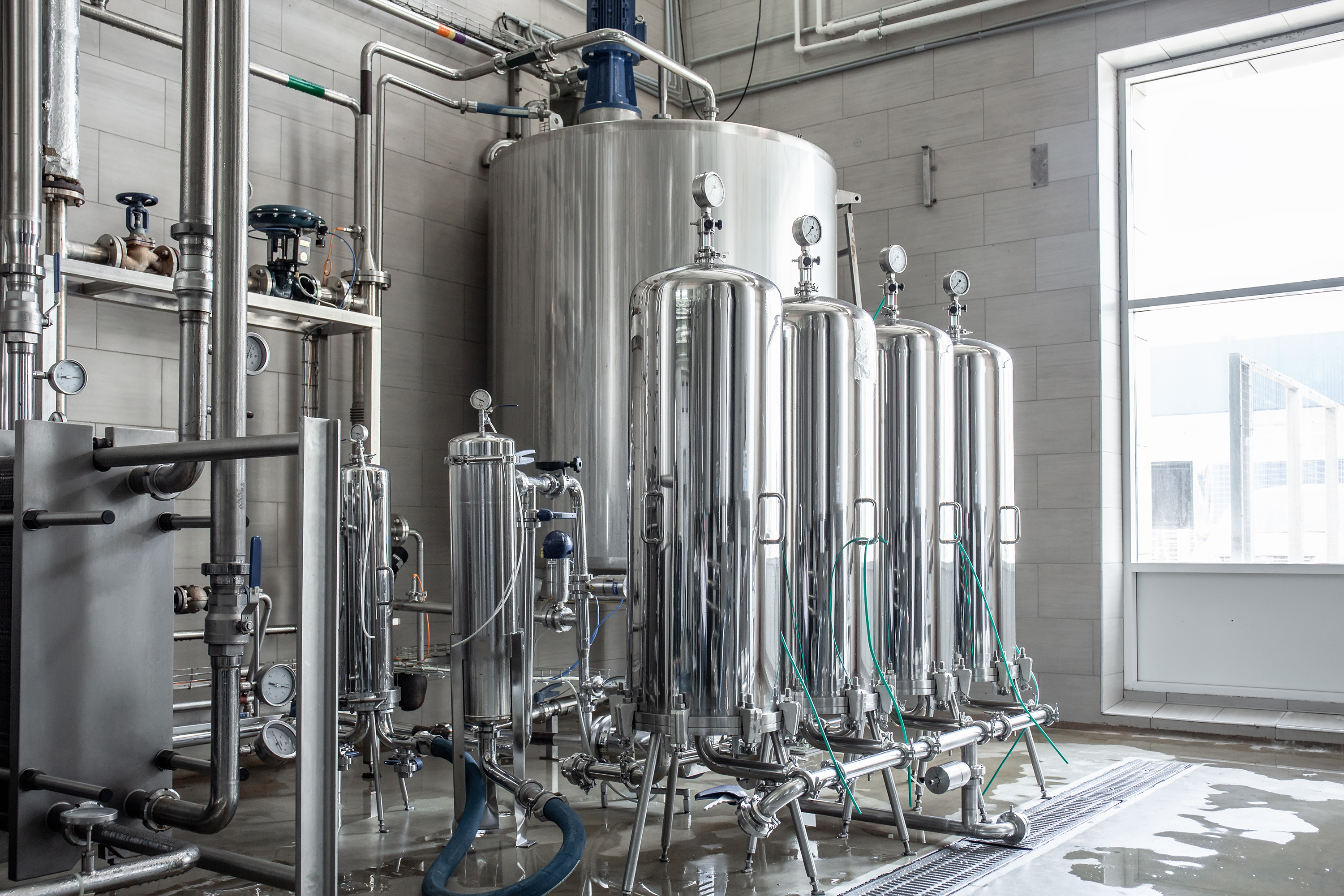
The role of filtration and bioprocessing in alternative proteins
Here we discover how Donaldson and its subsidiary, Solaris Biotech, are providing advanced solutions that ensure regulatory compliance, process efficiency, and product integrity in fermentation-based production, in doing so supporting the seamless scaleup of alternative proteins
The introduction of new ingredients – ranging from soybean roots and mushroom stems to fungal spores and other plant-based sources – has led to the development of novel processing methods, often incorporating fermentation. In this arena, maintaining sterility and controlling microbial activity are essential to achieving consistent results. However, while production techniques evolve, stringent food safety regulations remain a constant requirement.
Donaldson’s expertise in filtration for food and biotech ensures manufacturers meet standards while securing future operations. And through Solaris Biotech, acquired in November 2021, it advances food production with bioprocessing solutions for seamless fermentation protein scaleup. “Our mission at Donaldson is advancing filtration for a cleaner world,” begins Dominik Michel, Manager of Business Development – Non-Alcoholic Beverages & Food at Donaldson. “With decades of global experience in complex manufacturing, we bring stability, scale, and expertise to develop cutting-edge technologies that enhance human health worldwide.”
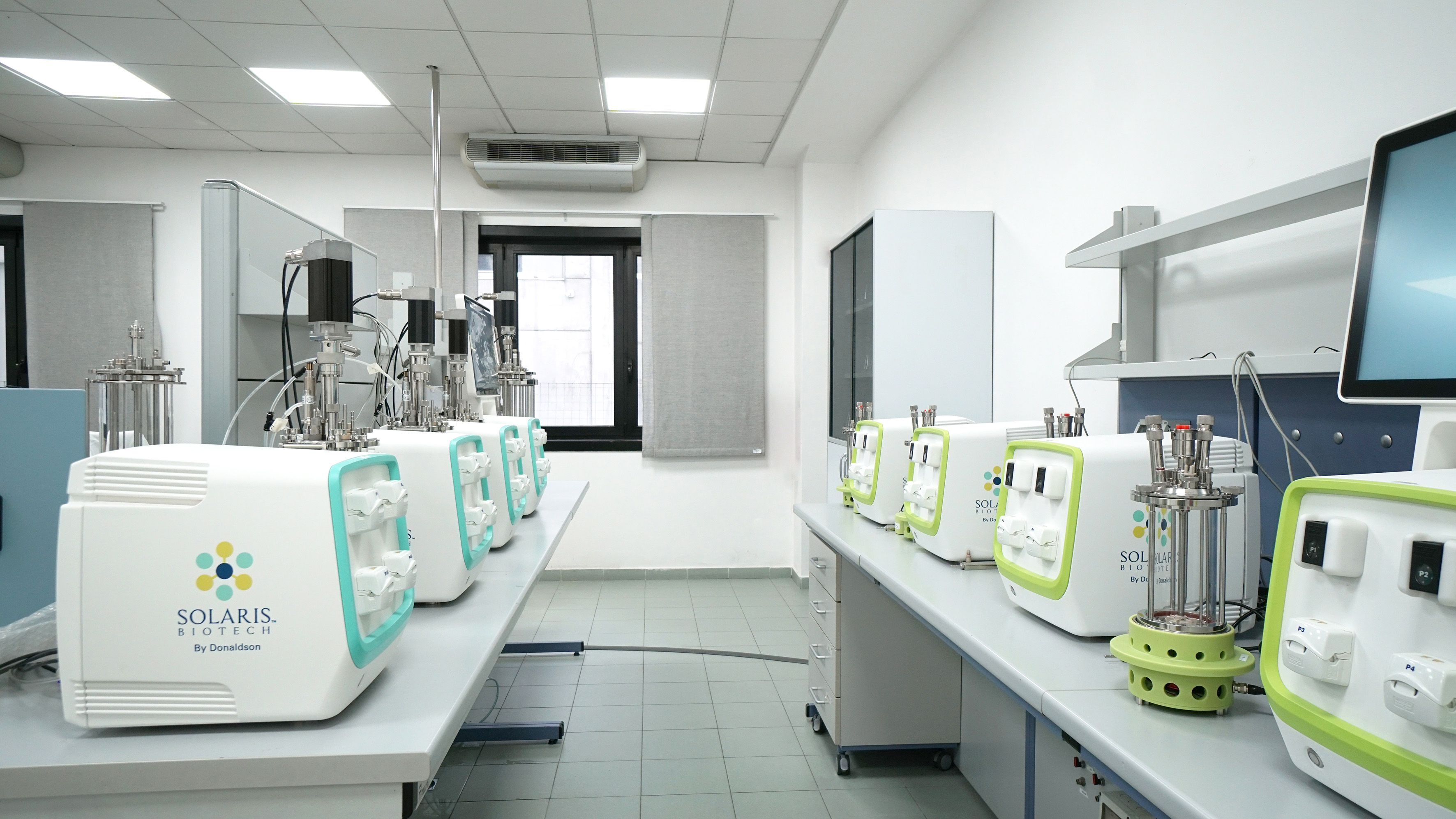
Filtering for efficiency
A well-engineered filtration strategy, suggests Michel, supports production efficiency while ensuring compliance with food safety regulations. Donaldson’s LifeTec filter elements, for instance, are designed for liquid, sterile air, and steam filtration to help manufacturers optimize the processing of plant-based and fermentation-derived F&B products.
As we all know, flexibility is key in biotechnology, hence Donaldson’s Solaris Biotech equipment provides scalable bioprocessing solutions, from small-scale development to full-scale manufacturing. Donaldson has worked with companies across the alternative protein sector, supporting the production of plant-based dairy and meat, fermented proteins, and cultivated ingredients.
Alternative protein production – particularly in precision fermentation and biomass fermentation – relies heavily on the integrity of bioreactors and utilities such as water, steam, and compressed air. These components require stringent contamination control to meet regulatory standards and maintain product quality.
“All regulatory frameworks – whether it’s FSMA in the USA, EFSA in Europe, or broader Current Good Manufacturing Practices – share the common goal of minimizing food safety risks,” Michel says. “To operate within these frameworks, manufacturers must implement preventive control measures.”
Regulatory compliance is key in alternative proteins, given the novelty of fermentation-derived ingredients. Precision fermentation cultivates microorganisms to produce functional ingredients, requiring rigorous safety standards to prevent contamination. Oversight is crucial from strain selection to downstream processing, with effective filtration ensuring sterility and compliance.
Filtration is not only about regulatory compliance – it also delivers significant financial benefits by protecting production processes and equipment
Filtration is a key method for contamination control in food, biopharmaceutical, and fermentation processes. Unlike thermal treatments like pasteurization and UHT, which inactivate microbes through heat, filtration physically removes heat-resistant spores, endotoxins, and particulates. Filtration, on the other hand, serves as a true removal step that ensures bacterial, particulate, and chemical contaminants are effectively eliminated at critical control points in the production process.
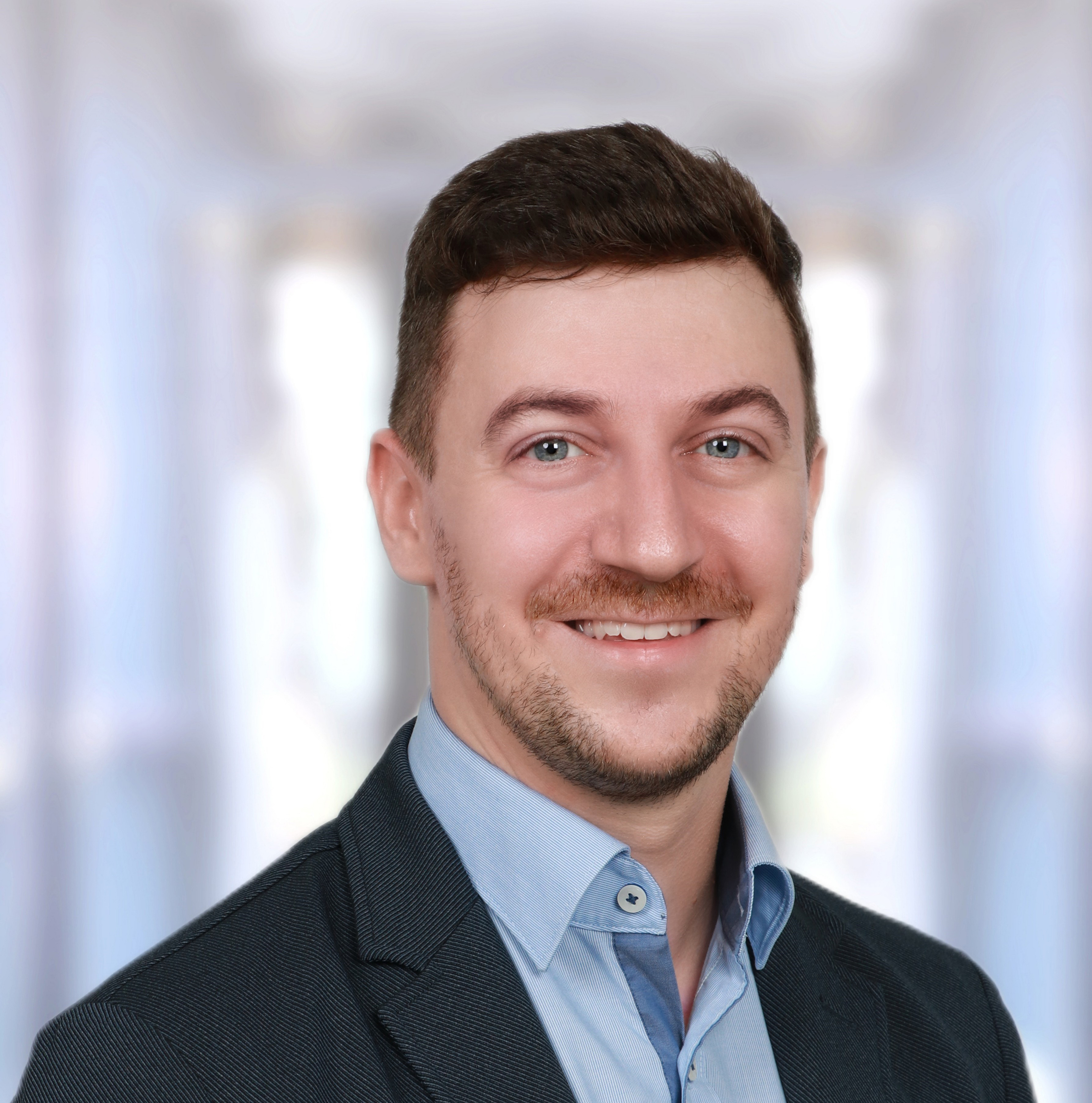
“Filtration is not only about regulatory compliance – it also delivers significant financial benefits by protecting production processes and equipment,” adds Michel. In industrial manufacturing, whether in food and beverage production, bioprocessing, or chemical synthesis, contamination control directly impacts both product yield and equipment longevity.
One of the most overlooked yet financially significant aspects of filtration is its role in protecting high-value processing equipment. Industrial machinery – such as fermentation tanks, heat exchangers, homogenizers, and membrane separation systems – represents “the largest capital investment in manufacturing facilities”, Michel reports.
Such systems are highly sensitive to fouling, scaling, and particulate buildup, which can lead to premature wear, unplanned downtime, and costly maintenance interventions. “Proper filtration ensures the longevity of these assets by reducing exposure to contaminants that could cause wear and tear,” Michel notes.
Filtration removes solids, microbes, and impurities before they reach critical equipment, preventing blockages, biofilm, and corrosion. Depth filters extend ultrafiltration and reverse osmosis membrane life, while sterile air filtration ensures aseptic processing. Oil and hydraulic filtration reduce mechanical wear, cutting repair costs and boosting uptime.
By implementing a well-designed filtration strategy, manufacturers not only safeguard product integrity but also enhance process stability and equipment reliability, which translates into lower maintenance expenses, reduced replacement costs, and increased overall plant efficiency, making filtration a key driver of long-term financial sustainability.
Seamless integration of water, steam, and compressed air is vital for alternative protein production, ensuring safety and efficiency. Water, used in processing and CIP, requires filtration to remove contaminants and meet regulations while extending reverse osmosis membrane life. Compressed air, crucial in food manufacturing, must meet ISO 8573-1 standards, with Donaldson’s filtration ensuring safety and compliance.
In direct or indirect food applications – such as sterilization, cooking, and aseptic packaging – steam quality must meet strict standards. Culinary steam, for example, requires filtration to eliminate contaminants that could compromise product safety. Michel emphasizes, “Filtration ensures that steam used in critical food production steps meets sanitary requirements, which reduces any potential contamination risks.”
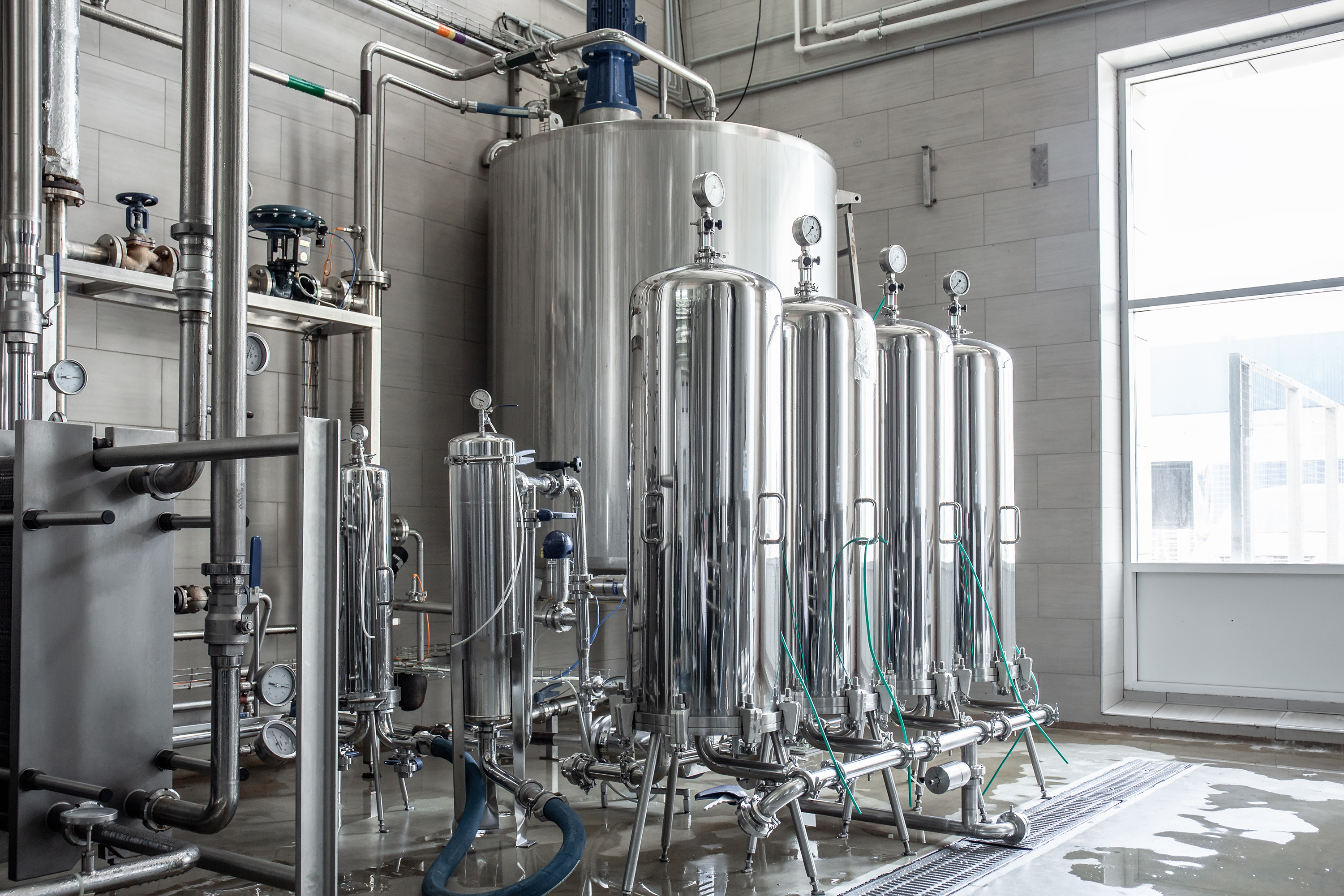
Ensuring sterility in bioreactors and fermentation processes
Sterility is crucial in fermentation-based alternative protein production, as even minor contamination can disrupt an entire cycle. Specific microorganisms, like yeast, bacteria, or fungi, must thrive under controlled conditions to convert feedstocks into proteins. However, fermentation’s warm, nutrient-rich environment makes bioreactors vulnerable to microbial intrusion. Maintaining optimal temperature, pH, oxygen, and agitation is essential, as contaminants from air, water, or raw materials can outcompete production strains, produce unwanted byproducts, or stress microbes, reducing yield and quality.According to Michel, the consequences of contamination in fermentation can be severe. If a foreign microbe infiltrates the bioreactor, for instance, it can rapidly multiply, leading to batch failure, costly delays, and potential shutdowns for extensive decontamination procedures. Beyond immediate financial losses, repeated contamination events can damage bioreactor infrastructure, compromise process validation, and require extensive troubleshooting to identify the source of microbial ingress.
“At Donaldson Life Sciences, we provide advanced filtration solutions tailored to alternative protein production,” Michel notes. “Water used in bioreactors must be filtered to a sterile level to prevent the introduction of contaminants. Similarly, the air and oxygen supplied to bioreactors must undergo sterile gas filtration to meet high ISO 8573-1 class standards.”
Storage tanks also play a crucial role in preventing contamination. Tanks used for reception, storage, and buffer processes must be protected with sterile air and breathing filters, ensuring that contaminants do not enter through air exchange.
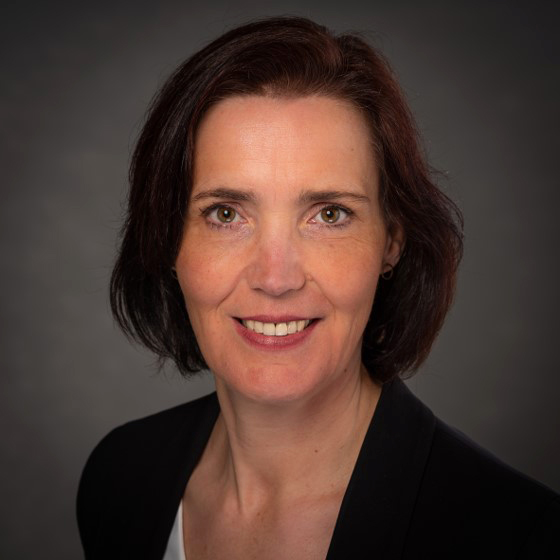
Bridging the gap from R&D to large-scale production
Solaris Biotech, a key player in Donaldson’s Life Sciences division, is at the forefront of bioprocessing technology, supporting companies in scaling up fermentation-based production. Katrien Verbrugge, Director of Global Sales Bioprocessing Equipment at Solaris Biotech, emphasizes the importance of seamless scaleup processes in alternative protein production.
“Our key contribution is enabling contamination-free scale-up from R&D to full-scale production,” she reveals. “By providing advanced bioreactors and fermenters tailored to specific needs, we help companies optimize their fermentation processes and produce high-quality alternative proteins efficiently.”
Solaris offers turnkey solutions spanning both upstream and downstream bioprocessing, ensuring a fully integrated production approach. “From feasibility studies and engineering to full-scale implementation, we support companies throughout their entire bioprocessing journey. Early collaboration is key to developing a well-structured scaleup strategy and ensuring cost-effective outcomes,” Verbrugge concludes.
Leveraging automation
To maximize efficiency and optimize bioprocesses, Solaris integrates advanced automation systems, including its proprietary software platform, ‘Leonardo’. This intelligent bioprocess management tool enhances scalability by enabling automated process control, experimental design, and real-time monitoring, making it especially valuable for fermentation-based alternative protein production. “Leonardo enables seamless operational oversight, ensuring that bioprocessing parameters are optimized at every stage, from R&D to large-scale production,” Verbrugge states. “This contributes to higher reproducibility, improved process control, and reduced variability in fermentation outcomes.”
As a central control hub, Leonardo integrates process parameters such as pH, dissolved oxygen, temperature, agitation speed, and feeding strategies. Through real-time data acquisition and predictive modeling, it ensures that optimal growth conditions are maintained throughout fermentation. By continuously adjusting environmental variables in response to live sensor data, it also minimizes process deviations and improves batch consistency.
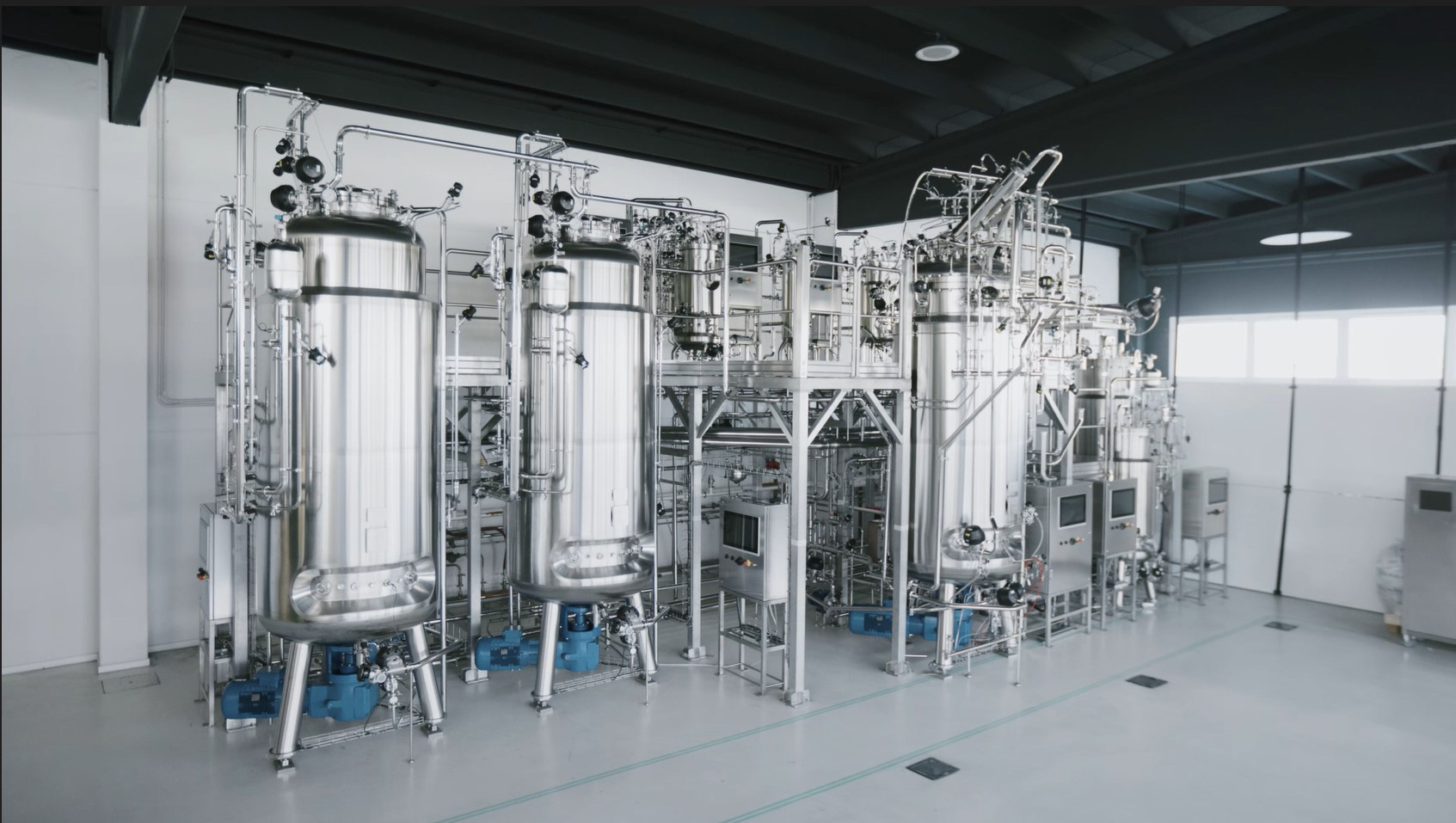
One of its standout features, though, is adaptive process control, which allows for dynamic modifications based on feedback loops. This is particularly beneficial where different microbial strains have unique growth kinetics and metabolic requirements. By automating feed profiles, oxygenation, and pH adjustments, Verbrugge suggests that Leonardo enhances cell density and product yield while reducing manual intervention.
The platform also integrates with advanced process analytical technology (PAT), offering real-time insights into microbial performance. This capability supports early detection of potential contamination, metabolic shifts, or deviations that could impact protein expression. As a result, manufacturers can proactively adjust process conditions before issues escalate, improving both efficiency and product quality.
For scaleup applications, Leonardo even provides digital twin modeling and data-driven experimental design. According to Verbrugge, these tools enable users to simulate different fermentation scenarios, optimize scaleup strategies, and reduce the number of costly pilot runs required before commercial production. The ability to correlate small-scale bioreactor data with large-scale production parameters ensures that process development is both rapid and reliable.
With a user-friendly interface and cloud-based accessibility, Leonardo supports remote monitoring and control, allowing operators to oversee fermentation processes from any location. This level of automation and connectivity enhances operational efficiency, reduces downtime, and enables real-time decision-making.
Sustainability and the future of filtration
Donaldson’s commitment to innovation and sustainability drives its development of advanced filtration technologies that enhance efficiency and protect the environment. This dedication extends to Donaldson Life Sciences and its growing role in alternative proteins through Solaris Biotech.
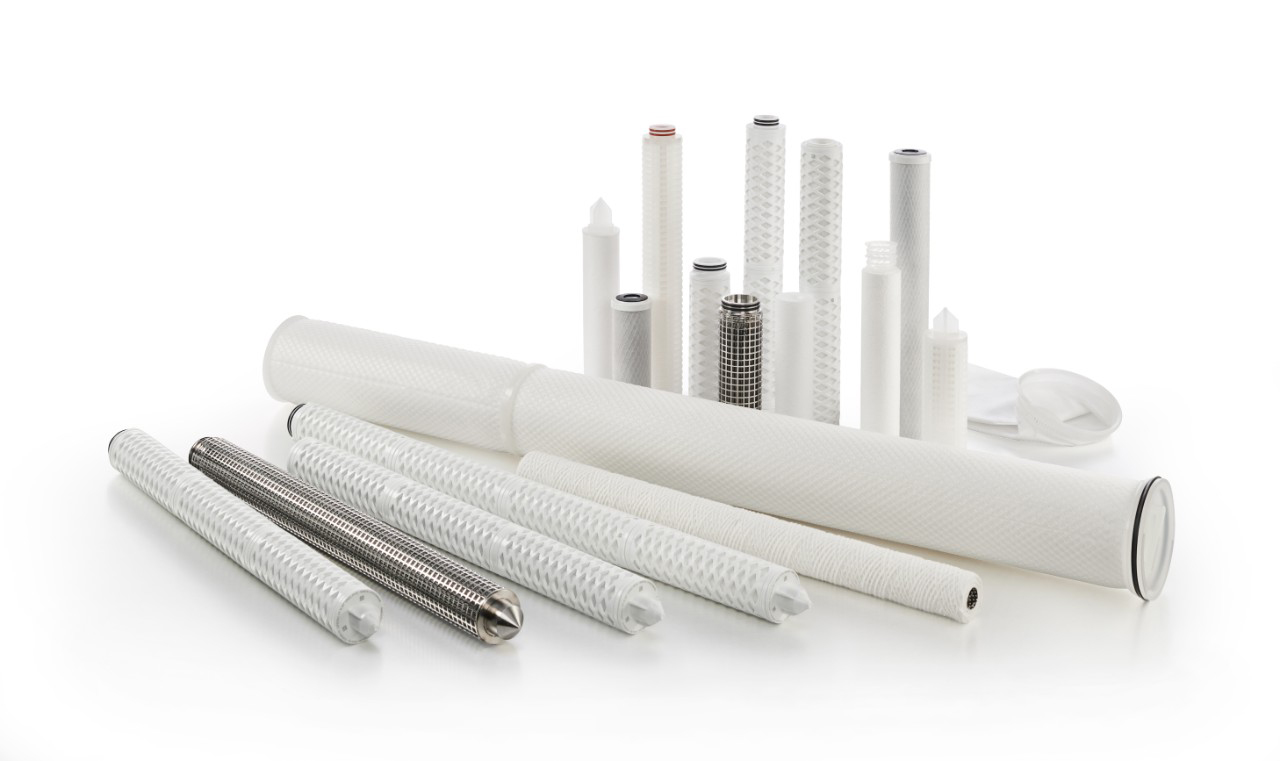
Verbrugge highlights, “Our mission is to provide advanced yet accessible solutions that deliver quality and flexibility,” reinforcing Donaldson as a trusted partner. “We strongly believe in alternative proteins and have developed a scalable bioreactor range tailored to our partners’ needs.
“Our vision is to support companies in enhancing sustainability,” she adds. By advancing fermentation-based food production, Donaldson invests in technology while shaping a more sustainable industry.
For more information visit www.donaldsonlifesciences.com
If you have any questions or would like to get in touch with us, please email info@futureofproteinproduction.com