

Manufacturing the food of the future
To transform our food system, we need more than science, research and good ideas. We need to be able to manufacture new food products at scale, bringing down their cost and making them accessible to more people. We need the manufacturing infrastructure to support the future of food – infrastructure that can be both capital and time intensive. Let us start by exploring what it takes to implement (build) this capacity.
For a first-of-a-kind or new process/product, which could include precision fermentation or other bioprocesses, we are trying to commercialize a food technology that has likely not been manufactured at scale before, so the technology itself is a major consideration. Think of the analogy of ‘building the plane as we fly it’. The technology has to be defined, or at least the process ‘frozen’, to proceed with detailed design. Using a common lexicon, the Technology Readiness Level (TRL) can help us understand the maturity of the technology itself, as we plan for the future. Once the technology has exited the research stage in the lab, it can move into the engineering phase in a pilot facility. This is a great opportunity to conduct experiments and understand how it will perform at a larger scale as it advances toward full-scale commercialization.
Once we have a better definition of the technology, or at least some assumptions and agreement on ‘freezing the process’, we can look at other considerations – things like location of the facility, sustainability, and capital and operational cost. Whether starting from scratch with a greenfield build – or leveraging an existing site/facility (brownfield) – site selection criteria covers various considerations of the location of a facility, and takes into account factors such as size of facility, labor (not just cost, but also availability), transportation and logistics, and utilities (infrastructure). When we talk about size of the facility, we have to think not only of current needs, but potential future expansion plans and the impact or constraints that site or facility may have on the future. Utility availability is a major consideration, particularly when a process is water, wastewater, electrical, or natural gas intensive, and coordination with the local municipality is a must. Sustainability is a consideration, whether it be renewable energy sources, waste reduction, or initiatives that provide a waste-to-value opportunity (for example, anaerobic digestion).
Particularly with sustainability in mind, integrating a TEA with a life cycle assessment (LCA) can help with an understanding of the economic and environmental impacts
In terms of costs, we must think beyond the capital costs of a facility. Even within capital costs, we need to consider beyond the equipment itself – a food manufacturing facility needs to account for sanitary operation, which includes design factors from architectural finishes to type and location of floor drains, as well as process utilities such as compressed air, process water, power, and wastewater. The facility capital costs, including these process utilities, should be expected to exceed the cost of the process equipment itself. Operational costs should also be evaluated – direct and indirect costs which generally include feed-stock/raw materials, utilities, labor, maintenance, waste disposal, and general facility overhead.
A techno-economic analysis lets us analyze the economics of the process by providing a good overall model which accounts for input and outputs. It can be used to evaluate economic feasibility and guide research and development (by narrowing in on and quantifying uncertainty and risk). The TEA process starts with a process design model, looks at the mass and energy balance, and incorporates the capital cost estimate and operating costs. Based on this technical and financial input, applying software modeling with a sensitivity analysis can provide insight and analyze profitability. Particularly with sustainability in mind, integrating a TEA with a life cycle assessment (LCA) can help with an understanding of the economic and environmental impacts. It is relatively inexpensive to perform a TEA, and these results can help direct where to spend more time on refining the process.
In future columns, we will explore some of these topics further – such as sanitary (hygienic) design, managing risk, infrastructure and utilities, trends in food processing and innovation, the engineering/design process, the importance of planning, and manufacturing strategy considerations (in-house versus contract manufacturing).
David Ziskind is the Director Of Engineering at Black & Veatch. He is passionate about helping new and emerging companies bridge the gap between science, engineering, and commercialization. This article was republished from the October/November 2022 edition of Protein Production Technology International, the industry's leading resource for alternative proteins. To subscribe to read future editions hot off the digital press, please click here
If you have any questions or would like to get in touch with us, please email info@futureofproteinproduction.com
More Opinion
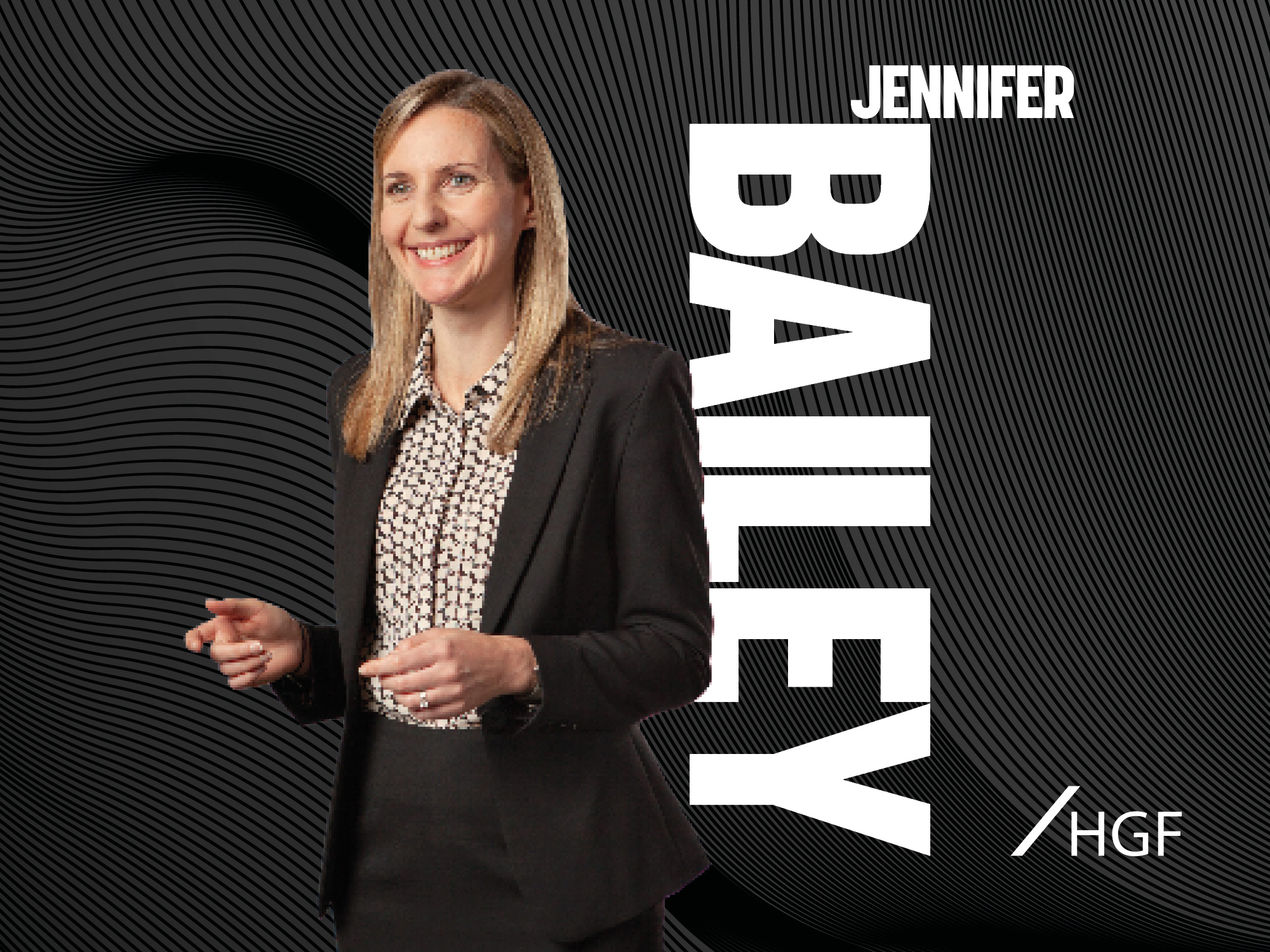
Trade secrets: when, how and why to use them

The criticality of conducting LCAs
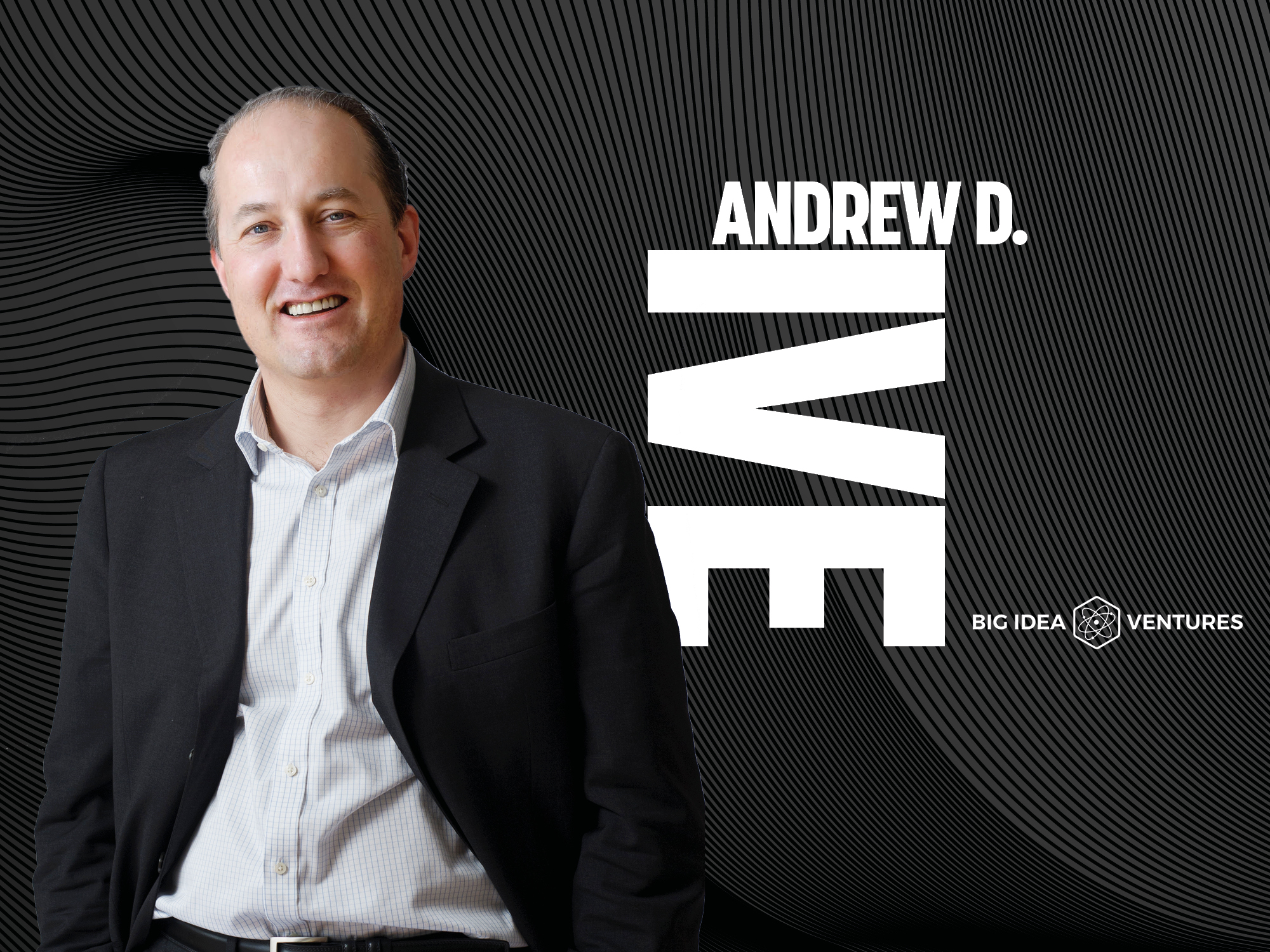
Creating a new protein sector: Part I
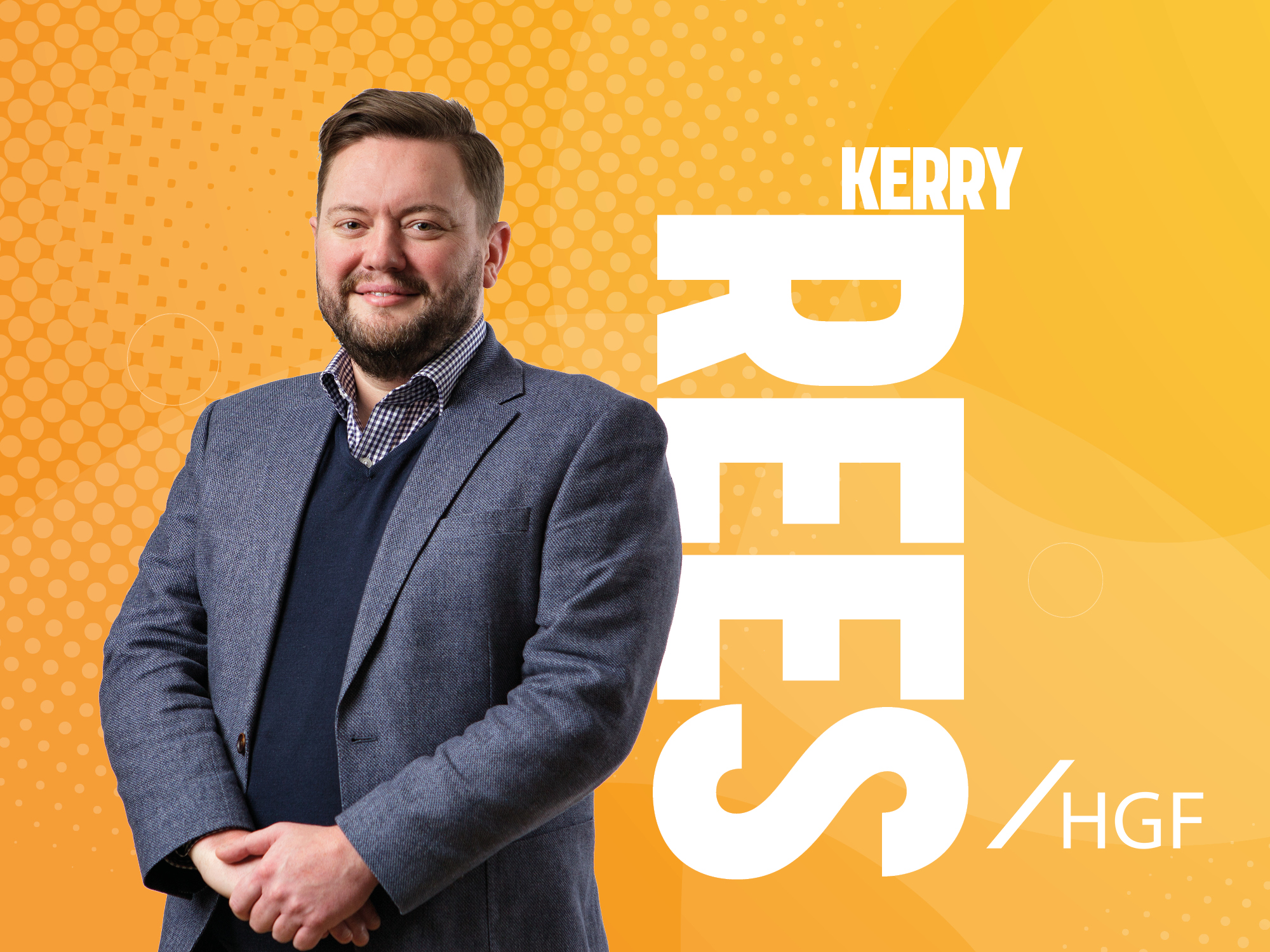
Protecting IP on a budget
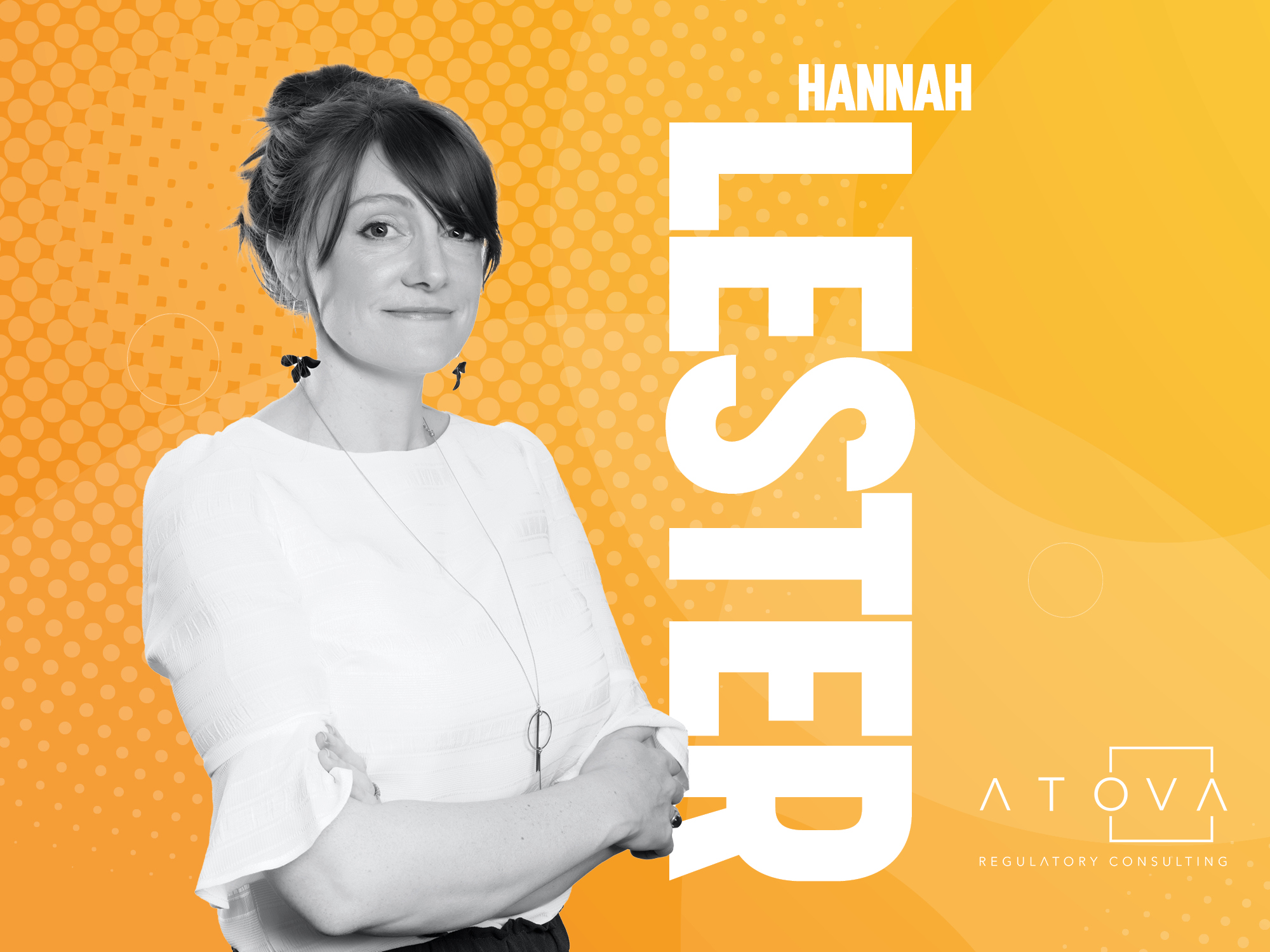
Will the UK become the new Singapore?
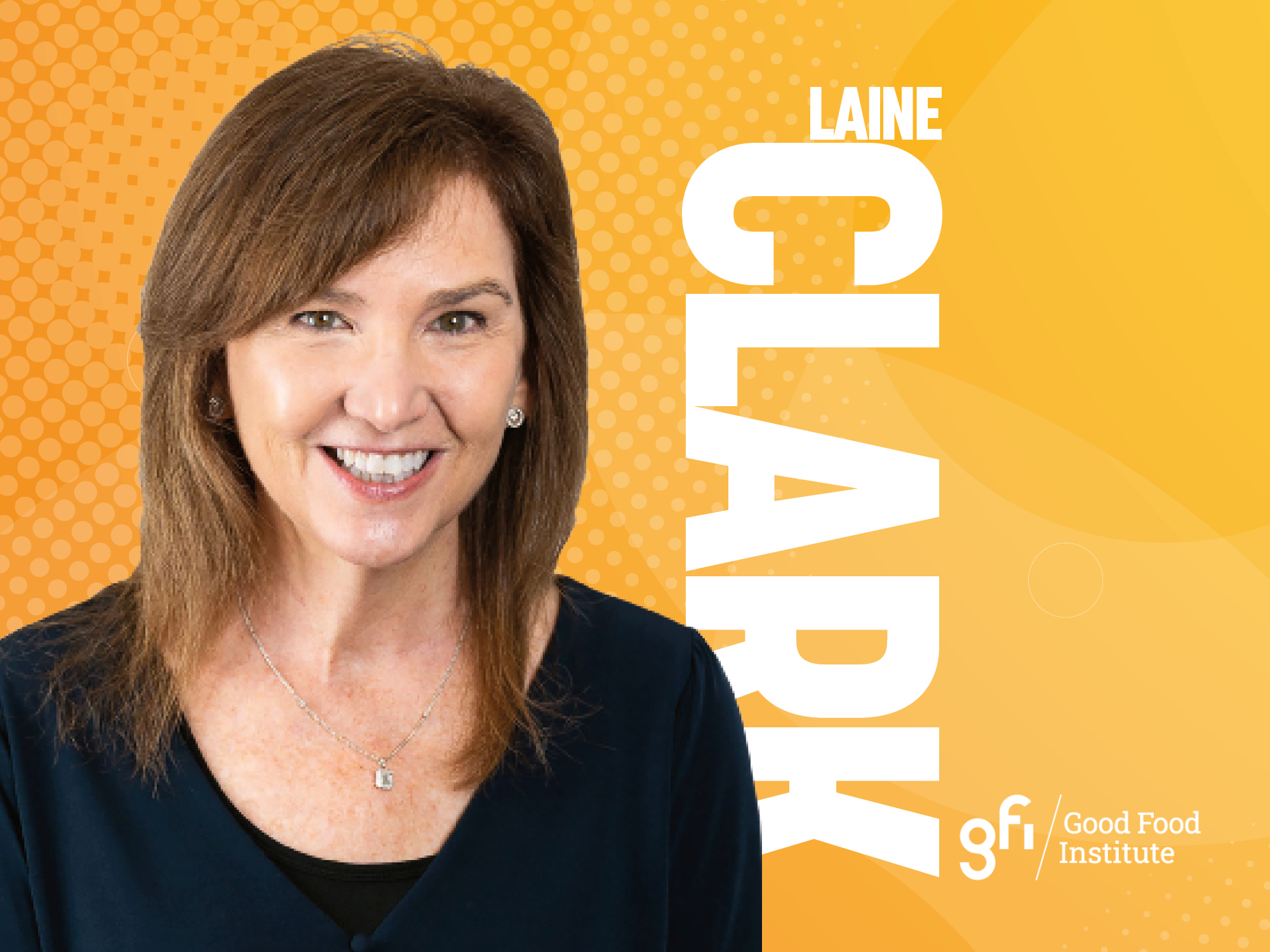