
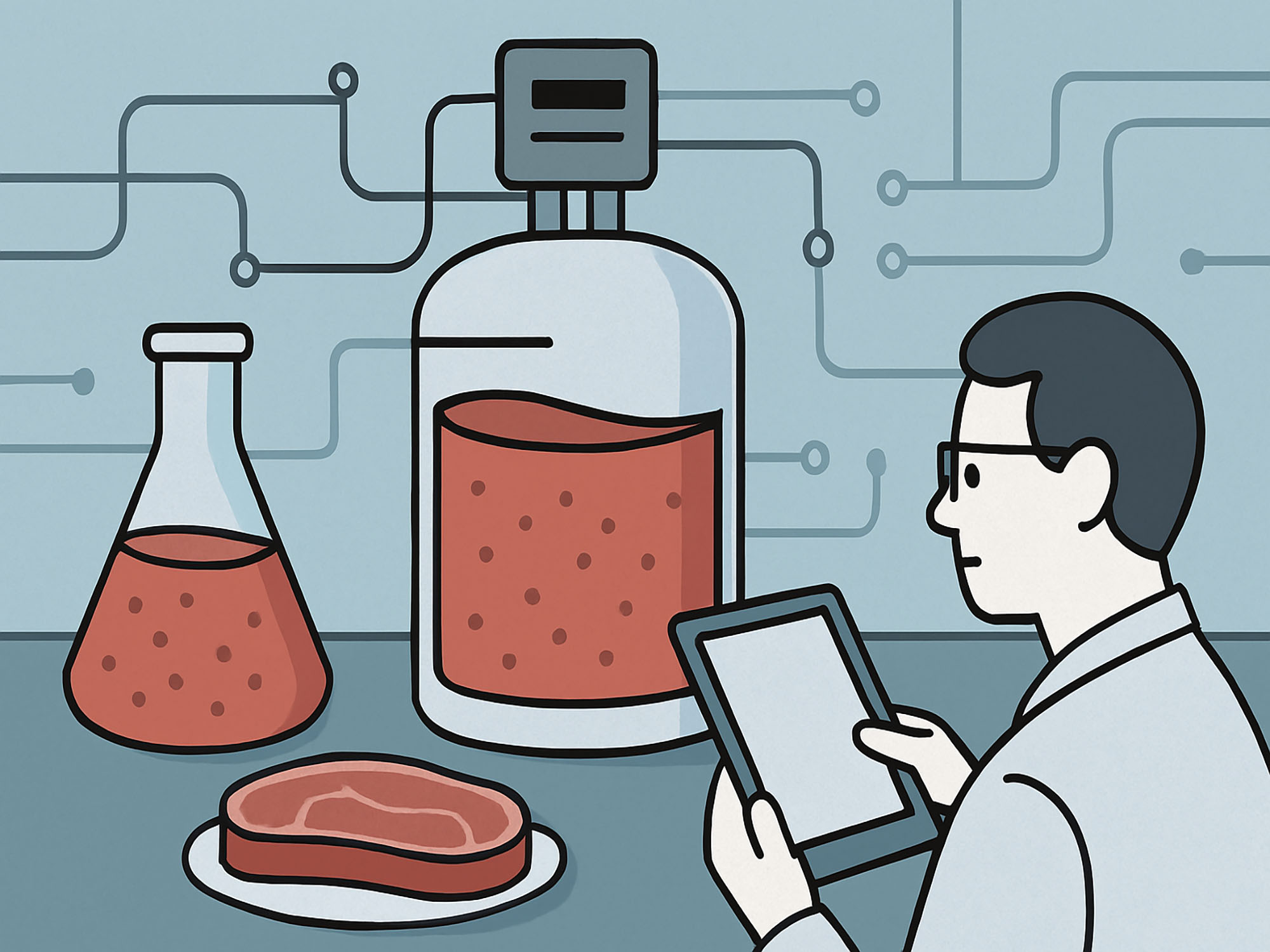
Second-generation cultivated meat startups surpass cost hurdles once deemed impossible
A new wave of cultivated meat companies is exceeding expectations around cost reduction, challenging long-standing techno-economic assumptions and reshaping what the future of the industry could look like. According to insights published by Lever VC, multiple startups have now achieved production costs significantly below the thresholds predicted by a widely cited 2021 analysis conducted by independent researcher David Humbird.
Humbird’s report, funded by Open Philanthropy, concluded that cultivated meat would struggle to ever become commercially viable, citing what he projected as insurmountable barriers in media costs and cell densities. At the time, he stated it would be “essentially impossible” for media costs to drop below US$1 per liter or for total costs of production to dip below US$16 per kilogram. In his most optimistic scenario, Humbird estimated media costs at US$2.50 per liter and production costs of at least US$21 per kilogram.
Just four years later, several cultivated meat companies are now producing cell mass using media that costs US$1 per liter or less, with some reporting costs well below US$0.50 per liter. These costs represent a 10- to 30-fold reduction compared to Humbird’s forecasts. In terms of production output, companies are also achieving cell densities of 60-90g per liter, exceeding the 60g per liter limit that Humbird projected as the maximum achievable in fed-batch systems.
As a result of these gains, total cost of goods sold (COGS) for cell mass production has fallen to between US$10 and US$15 per kilogram, with some companies operating below the US$10 mark. These achievements have been verified by Lever VC across a range of firms in the sector.
Crucially, these reductions have occurred without large-scale infrastructure or significant government subsidies – two elements that were vital for cost declines in other sectors such as solar energy and electric vehicles. The cultivated meat startups have relied instead on targeted R&D investments, process innovation, and pragmatic product design strategies.
A key contributor to cost reduction has been a shift in product design philosophy. Rather than pursuing fully structured, bioidentical cuts of meat, second-generation companies are focusing on hybrid formats. These products blend cultivated cell mass with plant-based ingredients, reducing the volume of cell material required. By optimizing the inclusion ratio – often using just 10-30% cultivated content – producers can deliver the desired flavor and texture while minimizing costs.
In tandem with hybrid products, many companies have pivoted to using undifferentiated or minimally differentiated cell mass. While mature animal tissues require complex differentiation, including muscle fibers and connective tissues, undifferentiated cell mass can still deliver flavor and mouthfeel when combined with plant-based matrices. This approach significantly reduces production time, complexity, and cost.
Another area of focus is media optimization. Several startups are producing growth factors in-house using recombinant protein expression in microorganisms, which allows them to avoid pharmaceutical-grade markups. These growth factors are being engineered for improved potency and stability, enabling lower concentration use while maintaining performance. Because cultivated meat does not require pharmaceutical-grade purification, lower-cost purification systems are sufficient, further driving down media expenses.
Reducing capital expenditures is the next frontier. Continuous production models and perfusion reactors are being explored to increase yield per reactor volume, effectively reducing the cost per unit of output. Perfusion systems, in particular, enable higher cell densities by improving oxygen and nutrient delivery while removing waste, though their implementation is more technically demanding.
Startups are also experimenting with modified reactor designs that substitute lower-cost materials, such as food-grade polymers, for pharmaceutical-grade stainless steel. While reactor hardware accounts for only a portion of facility costs, reducing these expenses remains an important step toward large-scale viability.
Taken together, these developments show that several cultivated meat companies are no longer constrained by the cost barriers once thought to be prohibitive. Though challenges remain, especially around scale-up and regulatory approval, the rapid progress suggests a more sustainable and commercially viable path forward than previously believed.
If you have any questions or would like to get in touch with us, please email info@futureofproteinproduction.com